An Innovative Approach Adopted by Kastamonu Entegre in Energy Management
A Move for Sustainable Production Through Smart Energy Management
A global leader in the wood-based panel industry, Kastamonu Entegre optimized its production processes by creating a digital twin of its MDF production line at the Gebze plant, as part of the EU-funded E2COMATION Project. Intended to enhance energy efficiency by real-time energy monitoring and advanced analysis techniques, the project provided outputs that would contribute to sustainable production by minimizing environmental impact.
In line with Kastamonu Entegre’s sustainability vision, the R&D and Innovation unit successfully completed a key project focused on energy management and efficiency — one of the company’s priority areas. Under the E2COMATION Project carried out by this team, a digital twin of the MDF production line in the company's Gebze plant was developed. The project monitored energy consumption on production lines in real time and optimized production processes using the data obtained.
Sole Turkish representative of the industry
Kastamonu Entegre is one of the few companies from Turkey simultaneously managing multiple projects within Horizon Europe — the European Union’s program supporting science and innovation. The E2COMATION Project, carried out under the TÜBİTAK-funded Horizon Europe program, was implemented to promote environmentally friendly production by improving energy efficiency in line with the company’s sustainability vision. The project tested the wood-based panel industry consuming high levels of energy and the food and beverage industries, aiming to monitor energy consumption on production lines in real time and optimize production processes using the insights obtained. Kastamonu Entegre was the sole participant from Turkey and the only representative of the wood-based panel industry among the participating countries. Completed over four years, the project focused on digitally modeling production processes and analyzing energy consumption data using advanced optimization techniques, with the aim of developing innovative technologies to enhance energy efficiency in the manufacturing industry.
Thriving practices, future goals
The initial trials of the solutions developed under the E2COMATION Project were successfully carried out at Kastamonu Entegre’s Gebze plant. Within the project, Kastamonu Entegre focused on the energy-intensive MDF production processes, monitoring the production line with over four thousand sensors. In addition to the use of heat and electricity, the project not only tested cogeneration systems that produce both simultaneously from a single fuel source, but also created a digital twin of the MDF production line. Using the digital twin that refers to the virtual model of a physical object, the intended tests could be carried out on the axis of benefits such as time, energy and cost advantages.
Optimal production enabled by digital twin technology
Through the digital twin application developed under the project, Kastamonu Entegre was able to simulate production transitions and observe their effects on product quality without the need for physical trials. At the same time, the virtual lab environment created by the digital twin enabled the company to produce energy-optimized solutions based on simulated outcomes.
The project also allowed for real-time monitoring of the company’s environmental impact. Thanks to the LCA tool developed within this scope, the environmental footprint of both products and equipment could be tracked instantly.
About E2COMATION
The E2COMATION Project was carried out with the participation of 18 organizations from eight countries and coordinated by STIIMA-CNR, one of Italy’s leading research centers. The project’s goal was to improve energy efficiency in manufacturing. Several prestigious academic institutions, including KU Leuven University in Belgium, contributed to this project.
As part of the project that pursued the goal of developing innovative technologies to enhance energy efficiency in the European manufacturing industry, production processes were digitally modeled and energy consumption data were analyzed using advanced optimization techniques, providing strategic insights for increased energy efficiency.
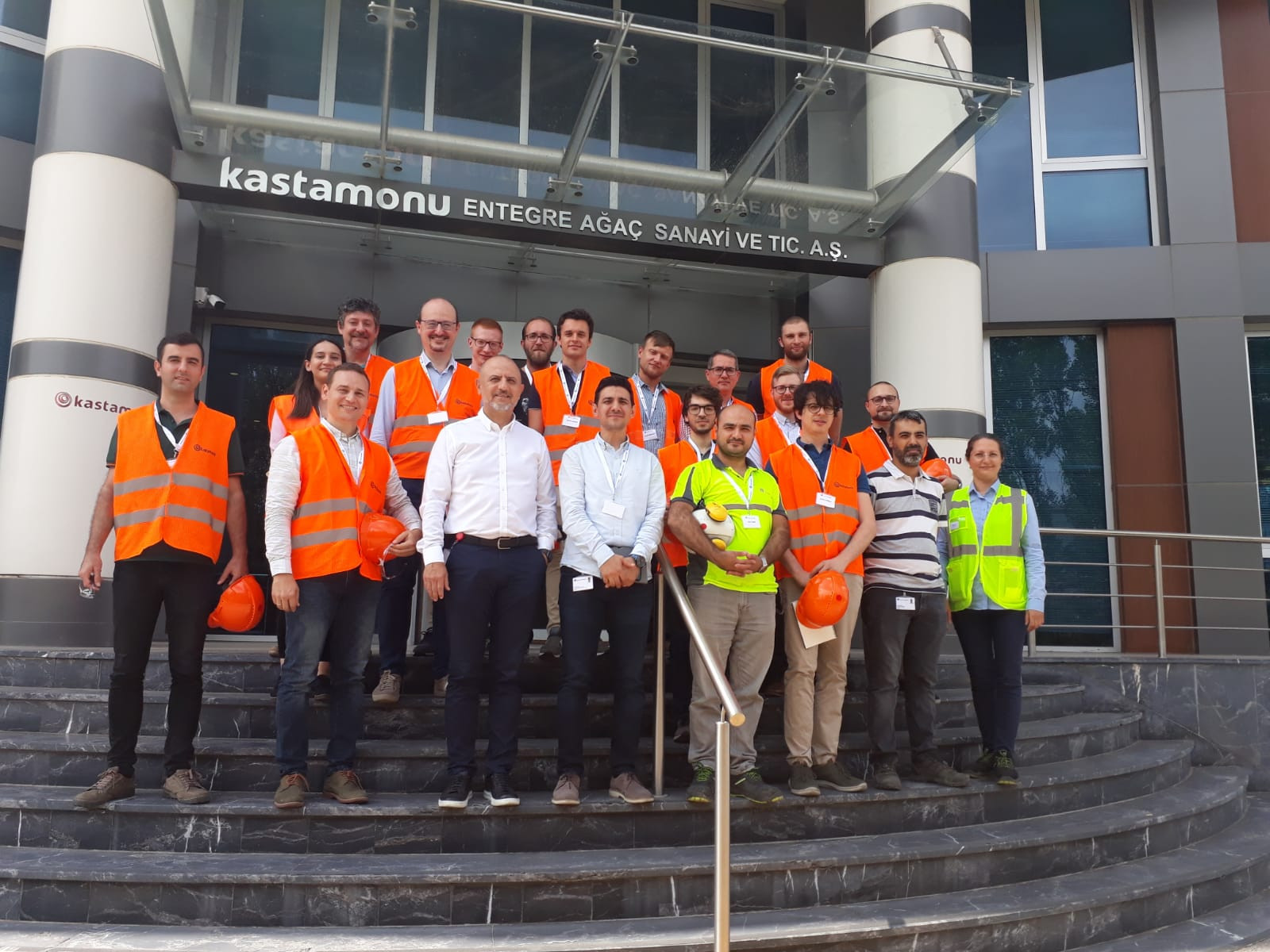